|
|
Job Location: Waco, TX
|
|
ABOUT THE ORGANIZATION: The Envases Group is a worldwide supplier of quality packaging solutions. The Envases Group is divided into three packaging divisions - PET Packaging, Aluminum Beverage Packaging and Food & Industrial Packaging - each with special competences within their field to serve customers the best way possible. Our core value is to supply high quality packaging solutions, always striving for growing our business in order to be the market leader in the markets we operate in. Envases Group is expanding global presence by the plan to open its first aluminum beverage can production and distribution center in Waco, Texas. The Waco operation will focus on aluminum beverage containers commonly used for soft drinks, beers, energy drinks, teas and non-carbonated beverages. Thank you for having interest in our employment opportunities.
REQ NUMBER: ENG-21-00013
CATEGORY: Engineering
EXEMPT/NON-EXEMPT: Non-Exempt
FULL-TIME/PART-TIME: Full-Time
NUMBER OF OPENINGS: 1
SHIFT: Days
POSITION: Maintenance Planner
Description
POSITION SUMMARY: The Maintenance Planner/Scheduler is focused on improving workforce productivity and work quality for a Manufacturing Plant by eliminating potential delays and obstacles through the planning process.
ESSENTIAL JOB FUNCTIONS: - Works extensively with the equipment maintenance software for setup, management and reporting of all equipment maintenance activities
- Reviews maintenance work orders daily to determine if any work orders from the present shift have been missed or not completed; notifies responsible personnel of deficiencies
- Runs daily preventive maintenance compliance report; for noncompliant work orders, sends email to the crew responsible for the work order and appropriate plant leadership
- Reviews notification orders and makes the necessary standardization changes to the naming of the notification to simplify future searches
- Meets with plant leadership to review severity and prioritize notification orders and makes updates as needed; acts as the liaison and coordinator between the operations and maintenance organizations
- Performs daily review of mechanic schedules to ensure 100% labor hours are scheduled
- Compares required parts list against available inventory and works with Purchasing Agent to ensure required parts are in stock prior to start date
- Supports the identification of critical inventory, optimal stock levels, Min/Max levels and obsolete parts
- Responsible for creating and maintaining comprehensive Preventative Maintenance (PM) plans in Computerized Maintenance Management System (CMMS) and ensures all PM routines are consistently reviewed and improved upon
- Add, remove or change work order text to support risk assessment (spreadsheet) and provides information to the EHS/Engineering department heads for review and reassessment of potential risk in preforming the task
- Creates new preventive maintenance work orders as needed which includes creating service types, task instructions, model work orders and PM schedules
- Documents work order creations or changes by maintaining the master tracker for preventive maintenance work orders and task instructions printed for use in the plant
- Runs reports and reviews cost by equipment for any heavy hitters and identifies potential cost saving opportunities; creates spreadsheet with required parts for a maintenance day and provides it to storeroom team members to ensure parts will be available 2 weeks prior to the maintenance day and/or contact purchasing to make sure parts are available before maintenance day
- Assists in creating SOPs for maintenance
- Trains team members how to use equipment maintenance functionality
- May assist in establishing, reviewing and monitoring maintenance budgets
- Tracks departmental Key Performance Indicators (KPIs) as identified and performs analysis for improvement
- Participate in the safety programs and/or committees; follow all site safety policies, company policies and procedures work safely and wear appropriate PPE
- Safely operate dolly, pallet jack, and/or forklift in handling supplies and equipment
- Maintain a clean and orderly work area
- Aide in training team members
POSITION REQUIREMENTS: EDUCATION & EXPERIENCE: - Preferred - Associates degree in Industrial Maintenance, Maintenance, Mechanical Engineering Technology or related field or two-year technical degree or equivalent; in lieu of degree a minimum of 2 years' experience serving in a maintenance planner or scheduler related role and industry plus the required experience listed below
- Required - High School Diploma or GED equivalent
- Minimum 2 years' experience in Manufacturing/Industrial Maintenance industry, production planning/scheduling, or Supply Chain Management or combined experience
- Prefer experience operating manufacturing equipment or machinery
- Prefer experience in inventory management along with shipping and receiving experience
- Prefer experience with ERP, SAP and/or MRP systems
GENERAL SKILLS/EXPERIENCE: - Demonstrated advanced expertise with Database software; Internet software, MRP software, Inventory and order processing systems; Project Management software; Spreadsheet software and Word Processing software.
- Strong background in maintenance planning for manufacturing; well versed at analyzing information, reporting investigation results, and have solid documentation skills
- Ability to influence functional leaders to support production volume and quality with strategy recommendations
- Ability to evaluate, select, adapt and modify standard manufacturing and plant quality techniques, procedures, and criteria
- Ability to learn operating principles and nomenclature of all assigned equipment, products and quality standards
- Ability to read and interpret blueprints, engineering drawings and materials specifications.
- Familiarity with the procurement of raw materials, standards, parts, and commodities
- Demonstrated skills in supplier operational and relationship management
- Forklift driver: Must receive training and be certified before operating a forklift; re-certification is required every 3 years
- Understanding manufacturing processes
- Prefer data collection and analysis experience in a high volume automated manufacturing environment
- Detail-oriented, ability to effectively handle multiple priorities, flexibility to reorganize and reschedule work on short notice to meet tight deadlines, have a strong quality mindset and enjoy working in a team environment; ability to maintain accurate, detailed records that will be audited periodically
- Ability to work on multiple projects at once with tight deadlines
- Must be able to identify and execute improvement opportunities through both process improvements and system improvements
- Ability to take ownership and responsibility with little direction
- Ability to effectively train people inside and outside their work group
- Proven ability to work collaboratively with others, friendly and personable
- Preference will be given to qualified local candidates
SOFTWARE/COMPUTER SKILLS & EXPERIENCE: - Intermediate level of knowledge in basic hardware and software using of a variety of different computer operating systems such as Microsoft Office Work, Excel, OneNote, PowerPoint, Visio, Google Workspace, Outlook/Gmail and web-site software required
- Working knowledge of ERP & SAP systems
- Working knowledge of Planning Systems
- Working knowledge of Warehouse Management Systems
- Has the ability to learn new software systems and data management systems quickly
- Proficient keyboarding and typing skills
DISCLAIMER: The above statements are intended to describe the general nature and level of work being performed by people assigned to this job. They are not intended to be an exhaustive list of all responsibilities, duties, and skills required of personnel so classified. Management maintains the right to assign or reassign duties and responsibilities to this job at any time. HOURS / SPECIAL CONDITIONS: Monday-Friday 8am-5pm; present to fulfill job duties & meet operational demands/support; schedule may vary depending on plant operational needs thus flexibility is required which could include long days, occasional evening & weekends; minimal travel for business meetings or trainings may be required; Regular and predictable attendance is an essential function of this position PM21
EOE STATEMENT: Envases Commerce LLC. is an equal opportunity employer and prohibits employment discrimination practices. All qualified applicants will receive consideration for employment without regard to race, color, religion, sex, national origin, disability status, protected veteran status or any other characteristic protected by law.
PI143201785
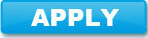
|
|
See all jobs in Waco TX
|